OLIVIA KRUEGER
Public Professional Work
Much of my work is still covered by NDA and cannot be shared yet. Please enjoy a look at some of the public projects I've worked on.

Engineering Consultant Internship
Blueprint Consulting, Additive Research Engineer
May 2019- January 2020
Stratasys & nTopology Collaboration
Engineering Consultant Internship
At the beginning of the technical relationship between Stratasys and nTopology, Stratasys was still trying to understand the possibilities and limitations of nTop Platform. I independently explored and learned the program to better understand the learning curve and skills required to make use of nTop's generative design features.
The images below show the development of a set of dice that I designed using nTop Platform. Click the picture to see the description of each step.
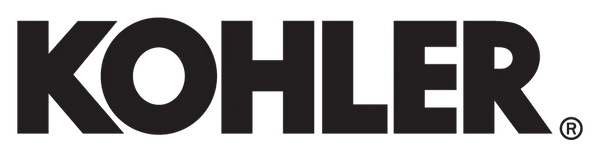
Mechanical Engineering Co-Op
Advanced Material & Process Development, Sanitary Engineering
May 2019- January 2020
Engineering Youth Apprentice
Kitchen Fixtures Engineering
July 2016 - August 2017
Rock.01 3D Printed Sink
Mechanical Engineering Co-Op 2019 &
Quality Engineering Co Op 2021
The Rock.01 sink was a collaboration between Daniel Arsham and Kohler to push the boundaries of the new ceramic 3D printing process that had been developed in house by a cross functional team of Kohler Engineers. While ceramic printing is not a novel concept itself, typical printed models consist of only one or two walls and mostly vertical form. The Rock.01 sink proved this method of ceramics manufacturing could move from artistic one offs to highly engineered production.
At first glance, utilizing a fused deposition modeling (FDM) approach for printing a thick clay slip doesn't seem like a complicated process. However, the challenges presented by the material are unique to vitrified ceramics. Vitreous ceramic slip is a thixotropic material, and because of this the material had a tendency to dewater as it was printing, losing the capability to bond to the previous layers. There were other issues as well, such as ensuring the clay would not slump under its own weight as it was printing, making sure the infill did not impact the aesthetics of the part when fired to shrink, and most importantly making sure the internal pockets of air could escape without causing the piece to explode in the kiln or no longer hold water when in use.
My role in this project was to handle early stage design for aesthetic and material parameter comparison, as well as slicer parameter optimization. When I returned for my third internship with Kohler, the product was preparing for an official launch, and I was able to continue to support the project by refining the internal infill structures, as well as the final slicer parameters to ensure the best quality sinks were produced.
Below are images of the final Rock.01 Sink that had a limited quantity release in December 2021.
Ironridge Cast Iron Sink
Engineering Youth Apprentice
The Ironridge cast iron sink began development in 2017, and was developed with the intent of producing the thinnest possible exposed edge of an apron front sink. One of the biggest challenges early on was to identify the optimal rim geometry and enamel thickness to minimize internal stresses in the glaze and thus maximize the durability.
I facilitated testing of samples with variables such as rim geometry, substrate surface quality, and enamel thickness. The collected data was compiled and organized to predict meaningful trends and suggest features that yielded a more durable rim.
Below are images of the final Ironridge sink that was launched in 2020.
All images of the KOHLER Ironridge Sink are from kohler.com